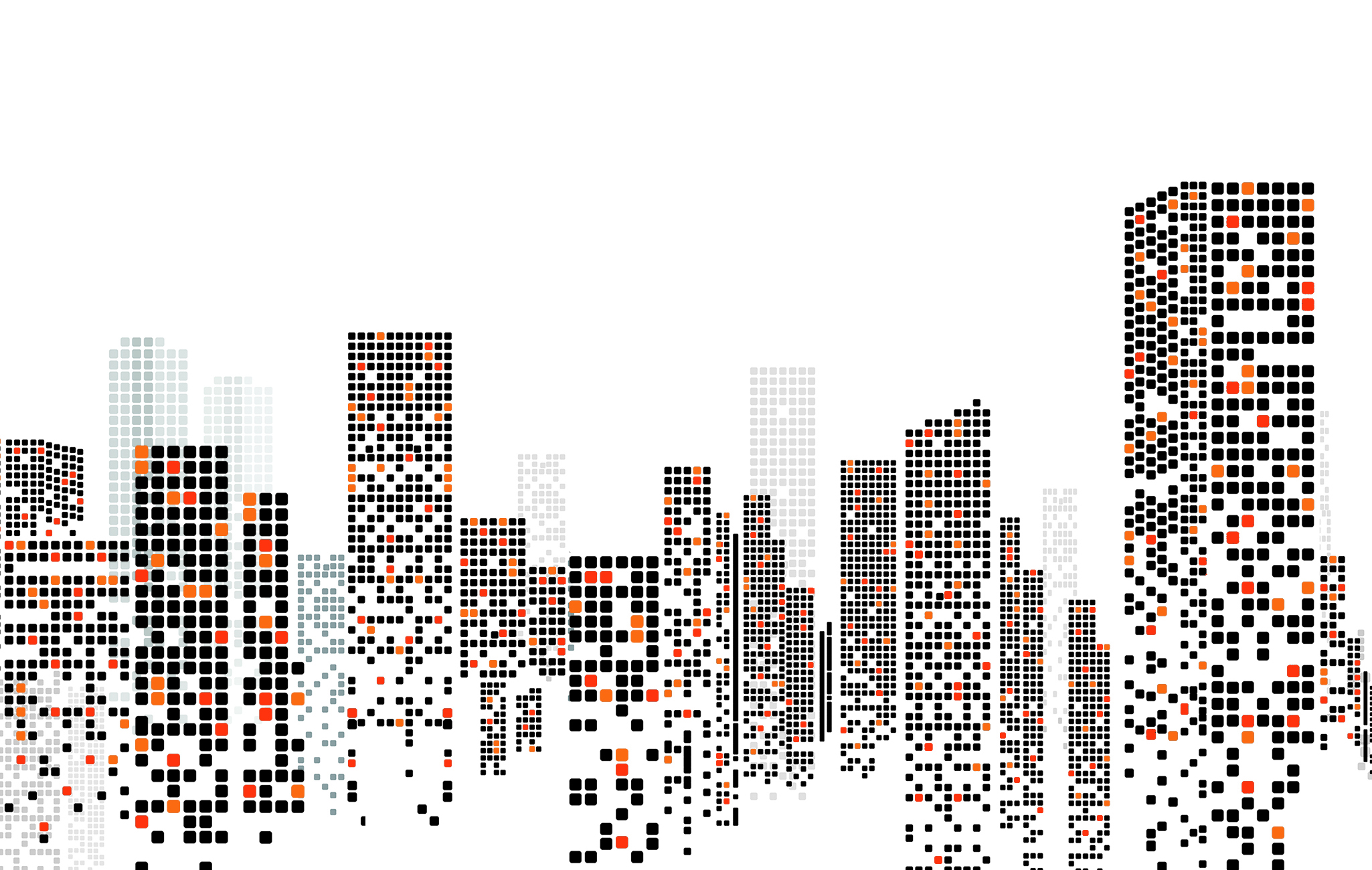
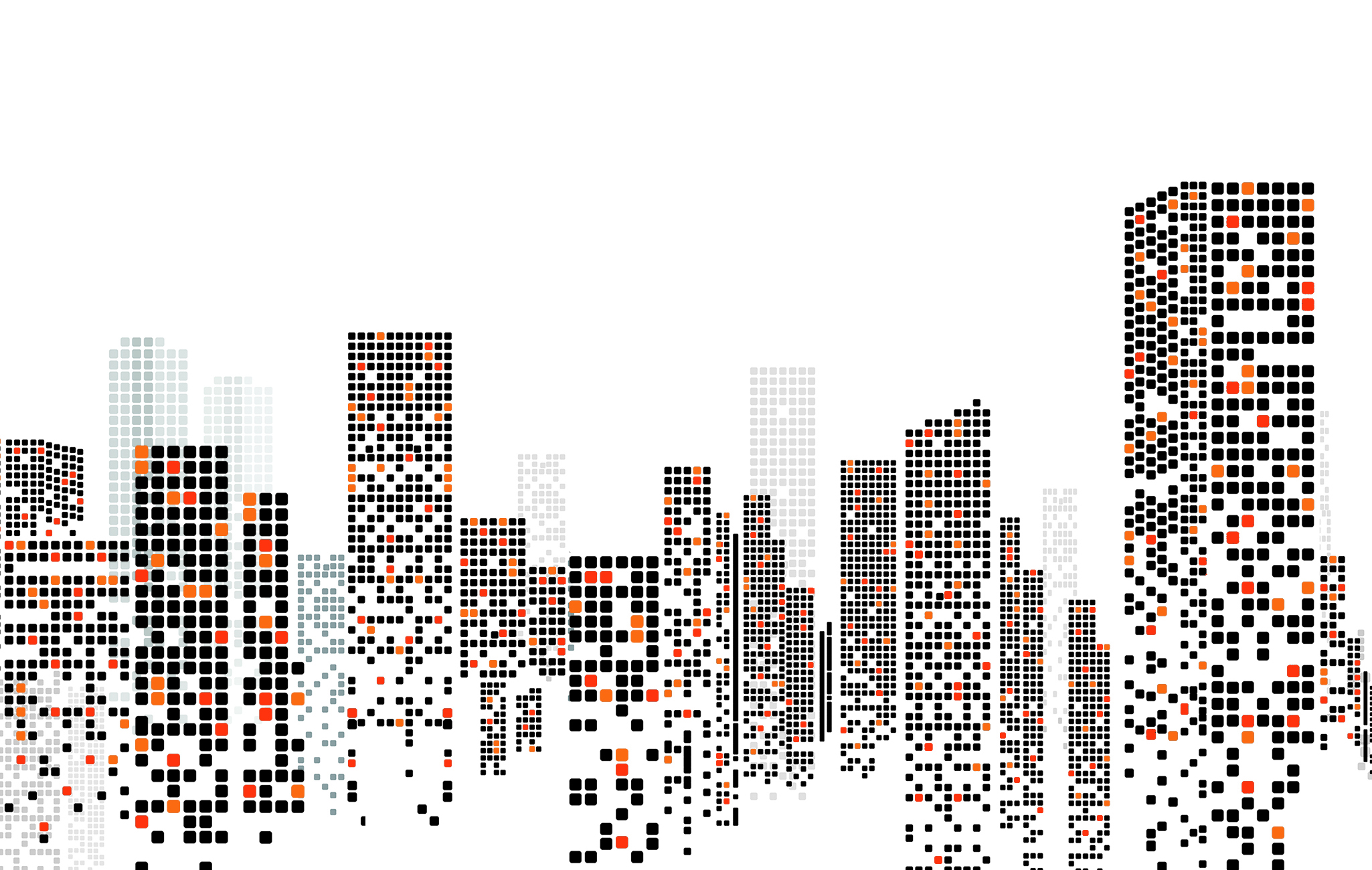
Buildings + Beyond Podcast
Podcast: Play in new window | Download
Kelly Westby, Commissioning Director, Steven Winter Associates, Inc.
Kelly Westby is the Commissioning Director at SWA. She works with developers, owners, contractors, and design teams to improve building performance in the New York City area and throughout the Northeast, and has completed energy audits on millions of square feet of existing buildings.
Kelly’s work also includes other aspects of new construction and existing buildings such as site inspections and energy modeling. She specializes in identifying and implementing practices to lower building life cycle energy costs, optimize capture of incentives, and improve operations and maintenance. She conducts on-site testing and verification of the effectiveness of green design and building methods. She also documents and communicates results, including specific recommendations for corrective actions. Kelly’s commissioning, energy code, and energy efficiency projects cover millions of square feet of commercial buildings across the five boroughs. Read more
As code requirements become more stringent around the country, the process of commissioning is more valuable now than ever before. Acting as third-party quality assurance providers, commissioning agents help building owners by improving the quality of construction and reducing maintenance and energy costs in the long run.
On this episode, Robb interviews podcast co-host, Kelly Westby, who is also SWA’s Commissioning Director. Kelly explains the importance of quality control on any project and describes how commissioning has evolved into a process, rather than a one-off measure.
Send your feedback and questions to podcast@swinter.com
Buildings and Beyond is the podcast that explores how we can create a more sustainable built environment by focusing on efficiency, accessibility, and health.
Buildings and Beyond is a production of Steven Winter Associates. We provide energy, green building, and accessibility consulting services to improve the built environment. For more information, visit swinter.com.
Hosts: Robb Aldrich | Kelly Westby
Production Team: Heather Breslin | Alex Mirabile | Dylan Martello | Jayd Alvarez
Kelly: 00:01
Welcome to buildings and beyond
Robb: 00:09
The podcast that explores how we can create a more sustainable built environment
Kelly: 00:13
By focusing on efficiency, accessibility and health.
Robb: 00:18
I’m Rob Aldrich.
Kelly: 00:19
And I’m Kelly Westby.
Robb: 00:22
In this episode I’m talking with Kelly about commissioning. Kelly Westby heads up our commissioning group here at Steven Winter Associates. And I’ve wanted to talk about commissioning for a while on the podcast, but it’s taken us a while to get to it. Kelly and I talked for quite a long time, which should surprise nobody who knows us, but we condense things a bit, so it’s a more concise discussion where we hopefully hit the high points. Kelly wanted to start with a good definition of commissioning.
Kelly: 00:54
So the ASHRAE guideline 0, the good old backbone of commissioning talks about commissioning as a process of ensuring that the building is designed, constructed, operated, and maintained in accordance with the design intent. And I like the definition, even though it’s a little bit wordy and a mouthful, and I can never remember the exact words, because it gets out a couple of different things that I think people miss when they’re thinking about commissioning. So the first thing is a process. So I think a lot of people think about maybe manufacturer start up as commissioning or you know, just a static or a one point in time test of a system as commissioning. But commissioning is really a process that’s applied to making sure that buildings are working properly. And that process, the timeline is, is part of that definition too. It’s from early kind of schematic design- predesign, through turnover, through into operation and can kind of move into continuous commissioning, which we can talk a little bit about. And then I like the ensurance part, it’s a quality assurance process, I say. And it doesn’t replace the quality control process that the general contractors need to be implementing throughout the project to make sure that things are being installed properly. It doesn’t replace that. It adds a layer of third party review kind of on top of that to make sure that the right quality control processes from the general contractor are kind of set up and being implemented properly. But we can offer a perspective of making sure that building systems holistically are operating properly. And I would say from an efficiency perspective for sure. But we’ve gotten a little bit in the industry. I think commissioning has gotten pigeonholed into the efficiency world alone because it falls in the efficiency category, the energy efficiency category and lead and because it’s required by energy code. But I think commissioning is so much more than that that it really has to do with like the guest experience, like thermal comfort acoustical performance. If equipment isn’t installed properly, it’s going to be very noisy and that’s going to impact the health and wellbeing of the people in the space.
Robb: 04:03
I probably would have said comfort and reliability. What are the biggest advantages, I guess, to an owner, and energy efficiency, certainly. But, you know, I think a lot of our clients that is secondary, you know, it has to be comfortable, it has to work, has to be reliable, and then we don’t want to, you know, use tons of energy. Would it make sense to talk about a somewhat specific example, like say an outdoor air system for common spaces in a multifamily building. Can you kind of give us a brief outline of what’s involved in commissioning something like that or a different piece of equipment? Or a different system I guess?
Kelly: 04:58
Yeah, I hadn’t thought about it that way. I like that being on this side of the microphone because I can just ramble and you have to make sure that I stay on track. So this is fun. So if we get brought in in the beginning, the question is, what’s the intent of the space? What requirements do we need to pay attention to for outdoor air? Are you going for LEED? Are you going for passive house? What does the system need to be providing? So we need to set the guidelines for what we need from that system, including reliability, like you said. Comfort. Is humidity Okay in this space, can it go as high as 85% or as low as 10%? Or do we need to keep the humidity in a certain range for comfort? Do we want the temperature to be in a certain range for comfort? Are we a typical New York where we’re not going to supply cooling to the corridors in maybe a smaller multifamily project or is it a luxury condominium and we absolutely are going to provide cooling to the corridors. And so we have to have those discussions up front of what’s most important to the owner. And so that’s what we call the owner’s project requirements. So that’s kind of step one. And then we look at the design and make sure that all the things that we outlined, whether it’s, you know, passive house and you need to have energy recovery, making sure that that energy recovery system is shown there on the drawings and is set up in a way that it can work properly, that the equipment is located in a way that one day the maintenance staff can actually access the filters and change belts and be able to maintain the equipment and to also make recommendations about is there a more efficient way to do this? Is there a better way to lay out the duct work so that you can reduce noise or you can increase efficiency of the equipment? And then moving on into submittals, making sure that the submittals are appropriate and match with the design intent and the owner’s project requirements are, and watching through construction to make sure that during the course of construction, the entire system, so the duct work and the components, are being installed properly, that the outdoor air unit on the roof is being mounted properly, that the clearance is actually provided there and the field, that things have been coordinated. So you don’t have, for example, a pipe hanger running through your duct work. Not that I’ve seen that specifically or anything. And then we, we look at trying to set guidelines for how that equipment then gets started up and we’ll review kind of the startup reports from the manufacturers representatives and that some people call commissioning. And so that can be a little bit confusing so that the manufacturer will come up, come out to the site and start up the equipment, which basically means kind of turning it on and checking some of the boxes. And they might go through a pretty thorough and rigorous review of what’s going on. Or a pretty simple review, then we’ll come out and make sure, run through all the tests, make sure the equipment will go into heating mode or cooling mode, dehumidification mode if that’s required. And make sure that it kind performs the way that it was intended to perform. The system then gets turned over to the operation staff. And so we need to make sure that the operators know what the equipment is supposed to do, first of all, what the design intent was. How to maintain the equipment, when to change the filters, when to change the belts, what other kinds of things they need to double check, how to do regular commissioning, which we talked about the different kinds of commissioning. Since I commissioned the building to begin with, then if the operator goes through and runs tests every six months or a year, that’s called recommissioning to add another word in there. And then the we can get into monitoring base commissioning. So if we set the system up to be what people like to call smart these days with a couple of sensors, maybe ]checking the power consumption on the fan in the outdoor unit, maybe checking the temperature out of the unit and we can monitor that over time and make sure that it doesn’t deviate from where it’s supposed to be.
Robb: 10:06
And I think that that one piece where you turn on the equipment, measure some power, measure pressures, measure flow, you know, that that kind of one time check when it’s just turned on. I think in a lot of people’s minds that is commissioning. But I appreciate you laying out, you know, there’s a lot that goes before and after that.
Kelly: 10:25
Yeah. And I recognize that it’s, it’s quite a process. There is quite a long process. So it can be, it can be difficult to describe, to take the time to go through that whole process. And I do think because we as an industry have thought about commissioning as kind of that manufacturer’s startup, that checking of those boxes. I think it is looked at as a slice in time, but I do think that’s changing. And actually there is a a study that, I’m going to blank on who put it together, but that looks at how many commissioning agents that are part of the building commissioning association now do continuous commissioning type work. And I think it was something like 60% versus a couple of years ago, maybe several years ago. You know, that number was much lower. And so I think a lot more people are thinking about how our buildings really operating after the normal routine of kind of, you know, okay. It’s not like all the construction people are gone now.
Robb: 11:41
Yeah. And I think there’s been a shift in commissioning, cause my impression, and correct me if I’m wrong, you know, it kinda was a necessary evil for LEED. It’s like, all right, you have to have somebody come in and do commissioning and you have to pay him, but we just need the commissioning box checked so he can get our certification. Like 10 years ago that was kind of the feeling I used to get about commissioning. Do you run into that? Have you run into that?
Kelly: 12:12
Yes. And I think it depends on who you talk to and I would say it also, it really does depend on the type of building in the industry. The other thing is now it’s not just LEED that’s requiring commissioning, but the energy codes are requiring commissioning now. So that’s a whole different level of checking the box that now gets, you know, the local government involved. And these requirements are all over New York City for example, is eforcing it versus other places in New York state where it might be required, but it’s not enforced. So then what does that even mean when it’s enforced? What exactly is enforced? You just need the little report or a little a one pager that says we received the commissioning report. And so I do think that there’s this opportunity for the market to respond by providing a very low quality service. Just like anything else, like local law 87 in New York City where it was required to do retro commissioning and energy auditing every 10 years. And we had an episode with Lori Kerr and she was kind of expressing some disappointment in the impact that that had made on, on the industry in terms of energy. And I think that a lot of building owners took that as, you know, another one of those New York city regulatory boxes that they needed to check. And I think that some similar things are happening in mid Atlantic region right now with the green code requirements and commissioning being required as part of that. Well, okay, I got to the permitting phase, the design is complete. I got to the permitting phase and they won’t let me get a permit unless you give me a preliminary commissioning plan. And you have to explain, well, you know, I’m not just gonna give you a plan, like we have to actually do commissioning if we create this plan. And luckily in those places they require it at the, the permit stage. In New York I’ve had folks call me and say, Oh, we need a commissioning report to get TCO. Can you give us a commissioning report this week? No, I can’t. There’s probably somebody out there who will, but then there are other owners that call us and they say, you know, I really think that I need another set of eyes on this building and you know, we need someone to do this commissioning thing.
Robb: 15:22
So for most of your work, are there code or program requirements? I mean, there’s growing code requirements, so
Kelly: 15:32
Yeah. There are growing code requirements and frankly LEED is required by code in a lot of places. So even some LEED projects are actually technically code projects. But it’s certainly a mix. A mix of different types of projects, different types of clients, different goals, and I do think commissioning, even ASHRAE says that, you know, commissioning is based on the owner’s project requirements. There’s always going to be differences in your process because of that, because it’s based on the owner. It’s not based on Kelly’s project requirements and I’m going to do commissioning my way on every project and if you don’t like commissioning my way, then go somewhere else. Potentially that is a method of commissioning. But I think that it is important to think about commissioning as finding the gaps in that particular project and figuring out how to fill those gaps. So for example, in some projects, everything runs through the general contractor and they are good about getting their subcontractors to respond to issues in the field and getting them to be on site at the right times. And other times we speak directly with the subcontractors, because that’s what’s appropriate on that job. And if I said I would never reach out to a subcontractor directly, I think that there would be some projects where I wouldn’t get traction. Now it’s, it’s a dicey relationship. We commissioning providers have literally no authority whatsoever. We don’t hold any of the contracts. Nobody gets paid by us. So we can get language if we’re brought on early enough, we can get language into the specifications that require subcontractors do certain things, but ultimately we’re not paying them. So there’s 1,000,001 things in the specifications and the con, you know there are some projects where not all million and one things get implemented on the job. So it can, it, this kind of trying to influence the project without having any authority is much more of a human behavior question than a technical question.
Robb: 18:20
Yeah. But that’s, I mean, I think that’s similar to all kinds of certifications. You know, I’ve, I’ve seen that I’ve been more involved in residential certifications, energy star, HERS ratings, but also leed, and you know, you’re not paying anybody, you’re a contractor to the owner or the architect or whoever it may be. And this is it. You report to the owner and you say, all right, check, check, check. We got something missing here that needs to be corrected. And then, you know, what the owner does with that or your client does with that will vary like crazy. But I think the best clients, you know, are organized enough, have their ducks in a row that there’s a method to, you know, get it done. You know, figure out who’s responsible and make sure that they address, address the gaps.
Kelly: 19:19
Yes, I do agree with you in some ways, but I would say that with a program, you’re either in or you’re out, right. And there’s a list of requirements and if you’re in, then you have to do those requirements. And that’s, that’s that. With commissioning, the owner gets to decide that ultimately. So it’s up to us. It’s more of recommendations along the way. The commissioning process is required by code and by LEED, but every little thing that we recommend is not necessarily.
Robb: 20:06
Gotcha. Yeah, no, that totally makes sense. That totally makes sense. I mean, even if you find some big gaps, you still have done the commissioning and then, and then the ball’s in the owner’s court as to how they want to use that information.
Kelly: 20:23
Yeah. And that question is super valid. I mean, do you ever end a commissioning project with zero open issues?
Robb: 20:32
Do you ever end a commission project with zero open issues?
Kelly: 20:37
Only if the owner accepts as is all the open issues and then they get converted to accept it as is. But yeah, I mean there’s like some things can’t be closed because, or I guess can’t be resolved because they got caught a little too late or it’s too expensive at this point to go back or there’s a lot of finger pointing along the way or they fired the mechanical contractor halfway through the job, you know, lots of things happen. So it’s not a perfect buttoned up process at the end unfortunately.
Robb: 21:14
So my first experience with commissioning, which I now know is should have been called retro commissioning. I was in grad school in the 90s and there was a new, very fancy new engineering building at the university of Colorado. And one of my professors got some funding to hire a grad student. I think it was first summer, it might’ve been first semester, to commission all the systems and there was a very fancy, advanced BMS with logging all kinds of variables everywhere. So I had the list of hundreds of points and my job was to go around the building and all the systems and measure with the second instrument, all of these points. So I was going through the air handlers measuring pressures and temperatures and humidities and doing Peto traverses and there was a structural stuff. I needed the money. It was a job. It was kind of boring. I’m just walking through what you know, is this really worthwhile? I’m just going through hundreds of points, hundreds of points, hundreds of points, very tedious. And I came to one of the air handler fans, like the main air handler fan and I was looking at it, it’s like, man, these pressures are high. And I had access to see what the control parameters were and the static was supposed to be set at one of the air handlers at 1.5 inches, it was instead set to 15 inches, which of course the fans couldn’t do. So the fans are screaming, the VFDs were pegged. And you know, I talked to the facilities guys and it was no big deal. It’s just a decimal point. And he just changed it. And then everything was right. But that was like right there. That paid for my time during this summer job, fivefold I did the math. And it was like, man, you really gotta you really gotta check. Somebody gotta check all this stuff. So it was pretty interesting, but, but that you would call that retrocommissioning right. The systems are in the buildings occupied. All right. Go in and see how things are working.
Kelly: 23:45
Yeah, yeah. And sometimes the line is blurry if the building just opened and then you realized that you should have commissioned it in the first place. And I wouldn’t stick to strictly to it if you’re, you know, going through and testing making a plan and testing systems and making it work properly. I think that sounds pretty good. But yeah, I think that that’d be more retrocommissioning. But it’s interesting that you said you know, you got excited when you found something. I thought about this a little bit before we started talking and people just love calling out other people’s stuff that they did wrong. Like it’s like human nature to just want to talk about what other people do wrong. I think it’s funny because we have the presentation that we, that we made into a podcast that you did with Steve, the top 10 design mistakes, right? If it was the top 10 things you should do in design, I don’t think as many people would be as excited about it. Right? So, yeah, so we do at commissioning conferences sometimes people do presentations on like trying to one up each other on weird stuff they found in the field and it can be hard to do over audio. Some of the weird stuff we find. But yeah, absolutely. 1.5 versus 15 it’s a small mistake because it’s one little period, but it’s a big mistake in terms of energy consumption.
Kelly: 25:48
We’ve seen toilet exhaust ducted to the wrong side of the ERB and supplying into the space. So you know, things happen.
Robb: 26:01
And nobody would discover that?
Kelly: 26:03 Yeah, until it started smelling weird. I’m not sure. I hope that they would, I’m not sure. And some of the energy stuff you really wouldn’t discover. So many, a lot of spaces have a heating system and a cooling system and those systems are separate but serving the same space and there’ll be operating at the same time. So you feel okay in the space because you’re being provided hot air to heat you up and then cold air to cool you down. So you’re on average, you’re okay. But you’re just running out those systems forever and spending rons on your, on your energy bills for no reason or your equipment is banging on and banging off all the time. So some things like that, some things you might notice, you might hear something when it’s operating improperly or you might feel uncomfortable, but you really have to go through the systems one by one step-by-step to make sure that everything’s working properly.
Robb: 27:04
Is any of that made easier or less time consuming or streamlined or whatever by newer technology, by smart systems, by IOT, I mean if you and the one of the HVAC contractors don’t go through the system step-by-step measuring pressures, measuring powers, measuring flow rates and instead all of this equipment gets installed. Can that lower the labor, lower the upfront time and as well as provide some down the road evaluation?
Kelly: 27:45
There’s potentially a bunch of software companies that disagree with what I’m about to say, but I think that maybe in the future, but I’m not sure that we’re there yet, Number one. Number two, I think that who commissioned then all of their sensors, I actually think you just added to the amount of time you have to be double-checking sensors in the field. The simplest system to check is like a one to one heat pump or you know, a packaged terminal key pump,
Robb: 28:17
Single speed on off. Yeah.
Kelly: 28:19
Yeah. The system’s right there. It’s not doing anything crazy. Oh, and by the way, it turns out packaged systems are actually more efficient than giant central systems, but we can save that for another podcast. I think we have this idea that if we say IOT and machine learning, then we can take humans out of the equation. And I just, I don’t think, I don’t believe in that philosophy. And I think that we are adding more and more sensors, more and more control points and that just makes the importance of commissioning even more because it’s not always going to be obvious what’s messed up.
Robb: 29:07
Do you have experience working with different engineers or different contractors repeatedly? Where it gets easier? I mean, did they come to appreciate you being there or, or other commissioning agents being there? Do you get, you know, a more streamlined working relationship or is it that the first time Every time?
Kelly: 29:33
That’s a good question. I think you should probably ask them, but I think, yes, I think the process does get easier. Oftentimes. The thing is, even if it’s the same engineer, it’s a different actual person, human being. So it might be the same engineering firm, but might be a different human being. Maybe it’s the same person, but it’s the combination of people are different or it’s a different system. so there are so many things that can change. And what I’ve really, truly been amazed by in my career and it, I call it job security, there is so many different ways that something can be messed up. So every time I think, you know, this isn’t something we need to pay as much attention to. Just like you said, you know, like, do I have to test every single sensor? Like, okay, packaged the packaged coil, like we talked about this a little bit packaged refrigerant oil, like the packaged unit. I’m not going to test the refrigerant charge in the field. It’s a package unit comes and you know, you install it and it’s fine, it turns out not always. So we, there was a catastrophic failure at a project that they kind of found later on that there was pinhole leaks and all of the packaged heat pump systems. Oh man. And they traced it back to a factory in Mexico that had just opened up and this was their first batch and they forgot about quality control or or whatever. But things like that can happen. Mistakes get made everywhere along the line and so it’s really important for, it’s important. I think for us as an industry now, I’m obviously biased, but to allocate capital resources to making sure those things are set up properly because like we were talking about hotels, if you put a guest in that space and it’s not working properly, you have to pay them back for that room probably under certain brands. Right.
Robb: 31:54
I sort of asked you this before. I mean with code requiring commissioning more and more, Are you seeing more buy in to the value of the process?
Kelly: 32:16
That’s a good question and I think that I might give you a little bit of a non-answer. The thing is I have been trying to make sure that we are having as big of an impact as we can have with the time that we have. And so we trying to move to really working with clients that, that are understanding the impact of commissioning and rather than rushing to open the building, which is reasonable, there is a large amount of money at stake if buildings don’t open it on time. But if we don’t set ourselves up with a proper plan from the beginning, then things can get behind and commissioning can look like it’s slowing down the process because it happens at the end. And with the code you need the sign off for your temporary certificate of occupancy. So it can be a very sensitive time for everyone. So I think that in some ways it makes the commissioning provider even more of the bad guy because you’re the one person holding up a C of O potentially. If you want to require something like for example, a bare minimum that they’ve at least started up their boilers. I would say there are some clients that haven’t, hadn’t necessarily done a lot of commissioning before and because it’s required, they’ve started to do it and they be grudgingly tell me that they are happy.
Robb: 34:13
So, so why do you like commissioning?
Kelly: 34:24
I like commissioning because you can look at a project early on and get an idea of what needs to be done and then follow that through to the very end of the project and see all the details then getting built around you and make sure that those things really work well really happen. I had worked in doing some energy auditing and you make a lot of recommendations and things may or may not go through depending on funding or other things. But 90% of the time that you work on a, on a commissioning project, the building will get built either way. And without you, it will get built in a crappier way, so you can definitely your energy is spent improving the built environment.
Speaker 6: 35:21
Thank you for listening to buildings and beyond. For more information about the topics discussed today, visit www.swinter.com/podcast and check out the episode show notes. Buildings and beyond is brought to you by Steven winter associates. We provide energy, green building and accessibility consulting services to improve the built environment our professionals have led the way since 1972 and the development of best practices to achieve high performance buildings. Our production team for today’s episode includes Dylan Martello, Alex Mirabile, and myself. Heather Breslin, thank you for listening and we’ll see you next week.