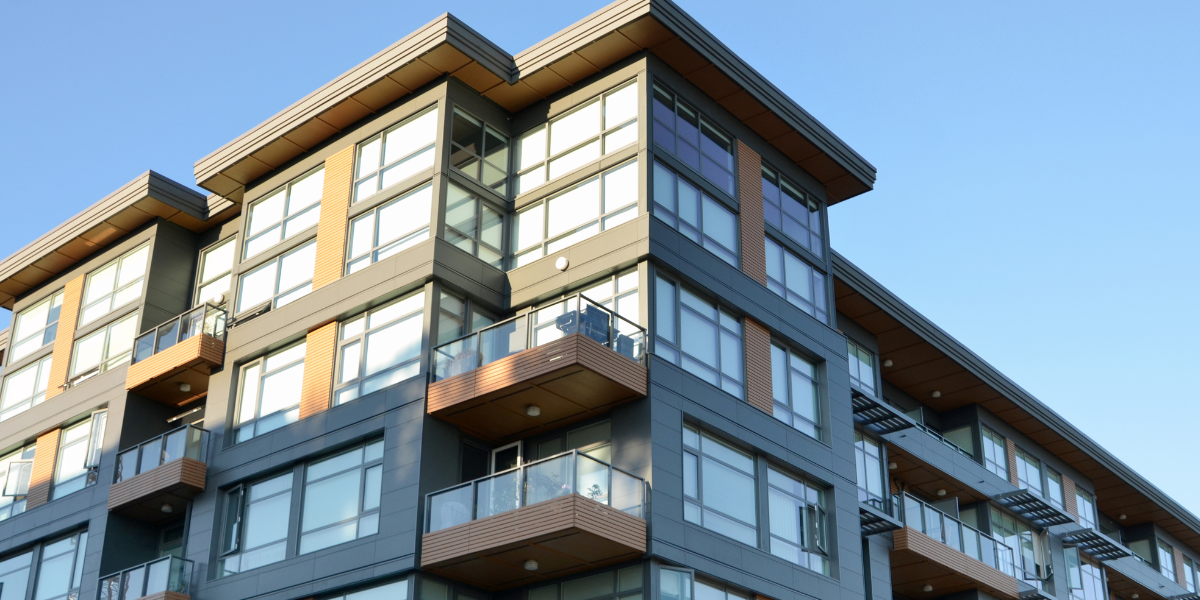
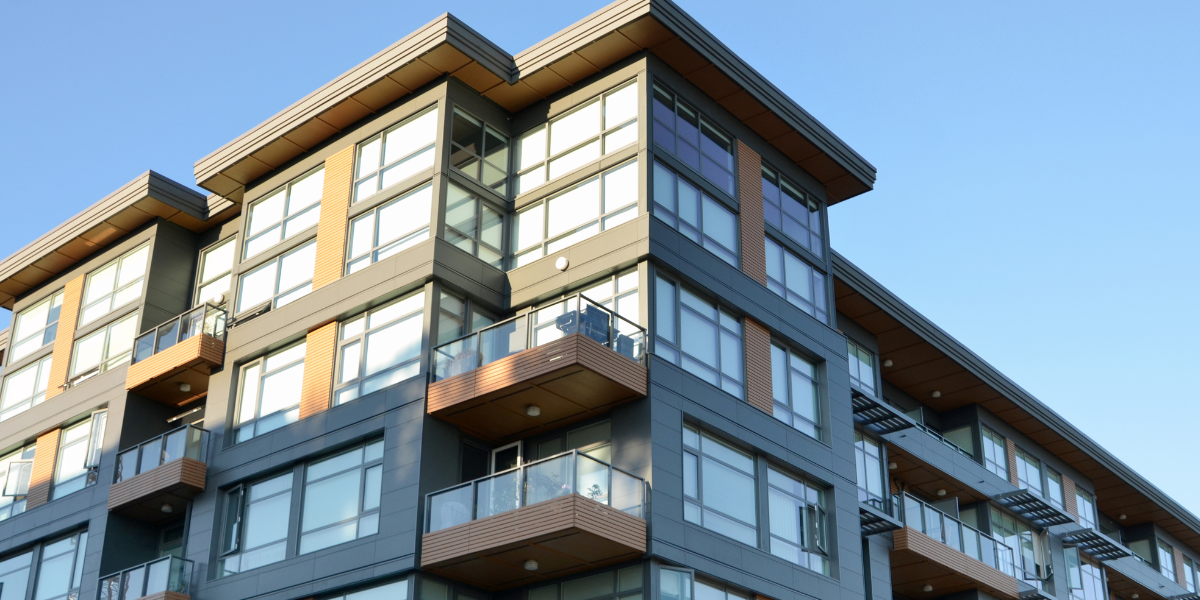
Blog
Explore data, resources, and tools available now to help project teams create a strategy to reduce embodied carbon along with operational carbon.
Building industry professionals have made great strides in reducing operational carbon, but without losing ground, we need to shift our efforts toward building materials and embodied carbon.
The time value of carbon is the notion that reducing carbon emissions now provides a greater benefit than reducing the same amount of emissions in the future. In other words, action today is worth more than tomorrow.
We can envision a future where all building materials have low or zero embodied carbon—even carbon-capturing ingredients—and there is a plan for reusing and recycling materials at the end of a building’s useful life. But how do we get there?
Read on to explore data, resources, and tools available now to help project teams reduce embodied carbon along with operational carbon.
There are several stages in a building’s life. The middle stage is when a building is in use, and it’s all about the operational carbon emissions that result from running—or using—the building. Addressing operational carbon has been critical to reducing greenhouse gas (GHG) emissions, and the building industry has made some progress. But important climate action opportunities are missed by focusing only on the middle stage.
The harvesting, milling, processing, and transportation of materials comes before the building use stage. And after the use stage comes the end of the building’s useful life, including how it can be reused or repurposed, or how its materials are broken down through natural decomposition. In these stages, it’s all about the embodied carbon emissions.
Before a building is even completed or occupied, all the emissions are embodied carbon from the construction process. In fact, it isn’t until a new building is roughly 30 years old that its operational carbon emissions are equal to its embodied carbon.
Architecture 2030 predicts that, with today’s business-as-usual, operational and embodied carbon emissions from buildings will be equal by 2050.
The World Green Building Council says that the two paths, operational and embodied carbon, need to merge now to meet its vision of net zero emissions from all buildings by 2050.
Global warming occurs regardless of how carbon emissions are generated, so taking a holistic approach across design, construction, operation, and reuse is critical to achieving zero carbon emissions from buildings.
The following building materials have high embodied carbon, but there are strategies and solutions available today to cut associated emissions.
Note that steel and aluminum also have high embodied carbon. Promote designs limiting their use, specify recycled content, support manufacturers who are transparent (those that provide Environmental Product Declarations (EPDs)), and look for sources aligned with climate action goals and certifications (i.e., Aluminium Stewardship Initiative, ResponsibleSteel™, worldsteel Step Up, Climate Active).
Concrete accounts for about 8% of global carbon emissions.
Market-ready solutions to reduce its embodied carbon—some published in RMI’s Concrete Solutions Guide—include:
More cutting-edge solutions include:
Insulation is approximately 10% of a building’s enclosure, and that enclosure accounts for roughly 20% of the building’s total emissions. There are several studies, including Efficiency Vermont’s The High Greenhouse Gas Price Tag on Residential Building Materials (PDF) report, that practitioners can reference to:
While thermal resistance is the main property of insulation, it can perform many other functions related to fire resistance, acoustics, moisture control, and air control. Human health should be a top consideration when choosing materials.
Avoid harmful chemicals and toxins and consider each product’s relationship to the durability of the assembly. This holistic approach is critical to advancing zero carbon goals without sacrificing healthy buildings.
Glass is used in a multitude of building products, including insulation, ceiling panels, roof shingles, floors, staircases, and of course, windows.
Due to the energy-intensive process of heating the melting furnace to shape glass, windows are high in embodied carbon. Low-emissivity (low-e) coatings, tempering, and laminating also contribute, but approximately 75% of the embodied carbon in an insulated glass unit (IGU) is from the flat glass.
The durability vs. embodied carbon trade-offs of triple-pane windows are as follows:
Pros:
Cons:
While the payback for adding triple-pane windows is only 20 years, windows are also a relatively easy replacement component. With advancements in heat mirror technology and gas-filled windows, new products will soon tip the balance on embodied vs. operational carbon savings.
Refrigerant used in air conditioning equipment plays a big role in ozone depletion and global warming. Transitioning to low-GWP alternatives enables the following:
Holistically accounting for embodied carbon in materials is the first critical step in assessment. Tools available for whole-building analysis rely heavily on EPDs:
While the RESNET Carbon Index addresses operational emissions by utilizing HERS software, a committee recently formed to develop an embodied carbon version of the index. Also, the Building Emission Accounting for Materials (BEAM) estimator recently became available and targets the rating community.
At a material level:
Benchmarking is critical to setting goals and achieving impactful results. RMI started this work by recently completing a study on 780 homes built to code in 2021 and 2022 in the US and Canada. The scope included the embodied carbon of structure, enclosure, and partition materials.
While there were extreme highs and lows, the overall average is 178 kg CO2e/m2cfa. The qualifier, square meters of conditioned floor area (m2cfa), is important for normalizing emissions for reporting purposes.
It’s notable that this study, like several analytical tools, excludes embodied carbon in mechanical, electrical, plumbing, appliances, and surface finishes. Further developing tools to include all components is significant, since GWP is high in finishes like paint, as well as the metal, glass, and plastics used in equipment and appliances.
Change can be made one product at a time, but there’s no time to waste if our industry is committed to big reductions in GHG and reaching our net zero goals.
Adaptive reuse and repurposing materials are good first steps to balancing operational and embodied carbon. Assessing a building’s potential for reuse or avoiding new construction are the best ways to reduce embodied carbon in our built environment.
While “the greenest building is the one that’s already built” may be a buzz-phrase being batted about, it is Carl Elefante who is credited with the phrase in his 2007 article in National Trust’s Forum Journal (PDF). If we had acted then with urgency, the time value of carbon reduction would seem less daunting.
Have questions about reducing embodied carbon in your next project? Fill out our contact form to speak to SWA’s experts.
Contributor: Karla Butterfield, Sustainability Director on SWA’s Residential Building Services Team
Steven Winter Associates