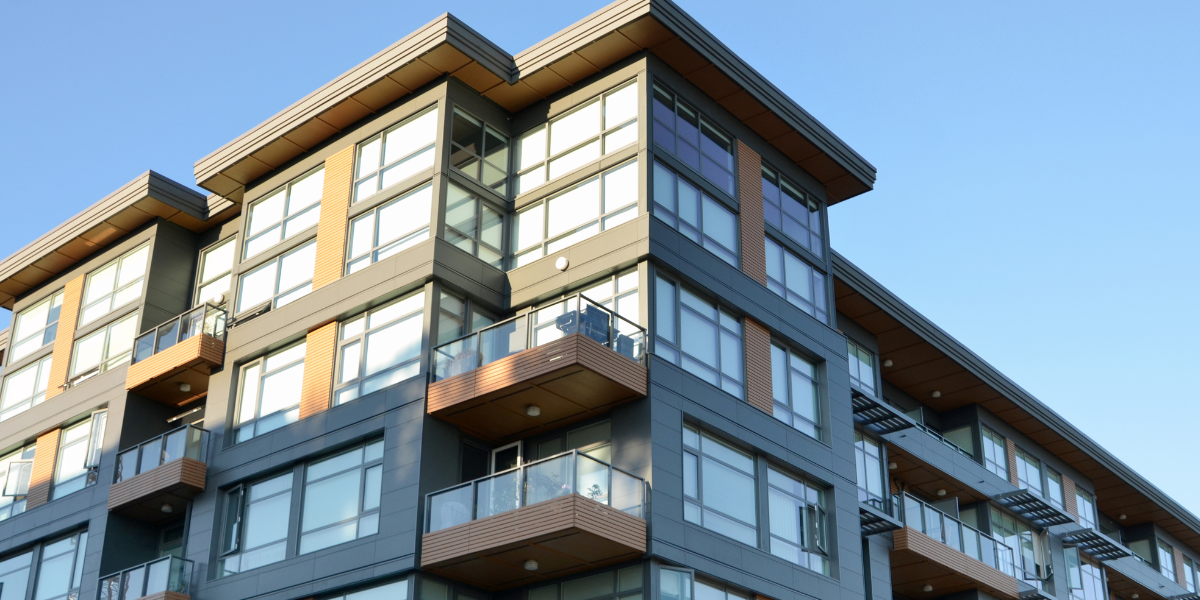
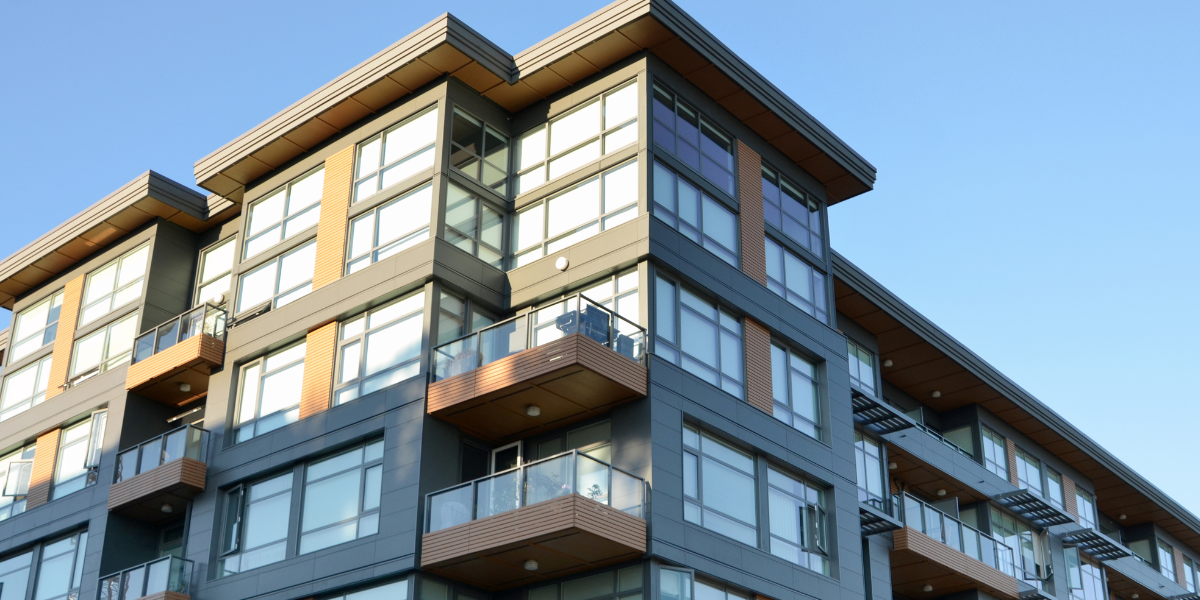
Blog
Carbon Footprint Analysis (a sub-set of LCA) takes into account all the carbon emissions (greenhouse gases put in the atmosphere), associated with a building or material from cradle to grave, i.e., to the point of recycling or disposal, and includes both embodied and operational carbon emissions.
In Part 1 of this blog post, we highlighted two of the most commonly used insulations in the U.S.– XPS board and closed-cell polyurethane spray foam – and noted that they are produced with blowing agents (HFC-based) that are putting more carbon into the air during construction than they save during building operation for many decades. We left you with a question: if we don’t use these insulations, how can we make up for the loss of the helpful qualities that has made us dependent on them?
One part of the answer comes from the development of new materials. In Europe over the last decade, Honeywell developed a new blowing agent, a hydro-fluoro olefin (HFO), which claims a global warming potential (GWP) of less than one, which is less than that of carbon dioxide. First in Europe, and now in the U.S., manufacturers such as Demilec and Carlisle are coming to market with a closed-cell polyurethane spray foam that uses this blowing agent instead of the HFCs that carry a GWP of well over 1,000. These spray foams have a slightly better R-value than their high-carbon predecessors, and otherwise have the same qualities that make them useful in multiple contexts – air/vapor barrier capability, conformance to irregularities and penetrations, etc. However, they also have many of the same downsides – high flammability, potential (and not completely understood) off-gassing post-application, and the basic fact that they are petroleum products.
Soy-based plastic spray foams, both open- and-closed cell, have recently been developed as lower-carbon, less toxic alternatives to HFC polyurethane foam. These are water-blown (GWP=0), and manufacturers claim they do not off-gas because they do not incorporate urea/formaldehyde. However, soy foams are still made with urethane as a bonding agent and can be as much as 85% urethane, so in the end, they are still a petroleum product with the carbon footprint and flammability that entails. The closed-cell versions have the benefit of acting as air/vapor barriers, but they have a significantly lower R-value (~R5 as opposed to R6.7-6.9) than the HFO/HFC blown polyurethane foams –. For this reason and overall scalability, manufacturers of these foams are competing in the residential/single-family market, not the urban high-rise market. There is also some controversy over the long-term dimensional stability of water-blown foam insulations.
Several expanded plastic insulations that have been on the market for decades are blown with low- or zero-GWP agents. For example, an expanded polystyrene (EPS) board (R3.9/inch) and polyisocyanurate foam board (R6/inch) is blown with pentane (GWP 7). Foil facing or vacuum wrapping has been used with these (as well as with mineral and glass fiber insulation) to provide a vapor barrier. So far, however, there is nothing on the horizon that replicates the combination of beneficial qualities of HFC-blown XPS insulation board, particularly for subgrade applications. Will it be possible to develop an HFO-blown version of the XPS board? Can mineral or organic fiberboard materials be wrapped or treated in such a way as to perform as effectively as XPS, particularly in a subgrade application?
Mineral fiber (wool), available in board, batt, and sprayable form, has become a common choice for sustainably-minded commercial construction in NYC and beyond. Aside from a serviceable R- 4, these products are fire-resistant to the point that they are routinely used as part of required firestopping assemblies. Mineral wool boards can achieve the same compressive strength as XPS board and are unaffected by water (they don’t slump or lose R-value), so they can be used successfully in similar applications, most importantly in creating thick layers of continuous insulation on the exterior of a building structure (below cladding or stucco). However, unlike SPF and XPS, mineral fiber insulations are not air or vapor barriers.
Fiberglass batt, the inorganic fiber insulation that not too long ago was omnipresent in both commercial and residential applications, has become less attractive as sustainability and more stringent code requirements increasingly drive insulation choice. Fiberglass batt’s lower R- 3.3, combined with its vulnerability to water or humidity, make mineral fiber batt the better choice thermally. Batts, in general, are becoming less and less useful because their intended use in interior stud framing cavities is now recognized to be a highly inefficient use of material. In metal framing in particular, batt insulation garners 40% of its nominal R-value at best and is liable to promote internal convection around the edges of each stud cavity. This is not a responsible or sustainable use of embodied carbon or operational carbon.
Mineral fiber is made from rock, and fiberglass is silica-based – both are therefore energy-intensive to manufacture and require removing material from the ground. Therefore, they can have high embodied carbon costs, which must also be weighed when using them.
Organic fiber-based insulations (wood, hemp, straw) have been more easily scalable to and used in single-family and smaller commercial or residential buildings, although there is excellent ongoing research and potential. The El Dorado behind organic fiber is the idea that with responsibly managed forestry or crop growth and low- or no-fossil fuel burning processing and transportation, many of these materials could be carbon negative in construction, meaning that they will ultimately result in removing carbon from the atmosphere (sequestration). There is every reason to pursue this line of development as vigorously as possible, but a complex array of factors makes organics not yet easily applicable to much commercial urban construction. Insulation developed from recycled/reused materials, such as post-consumer cellulose, denim and plastic are also in this category.
Lots of options, but designers must still understand the critical implications of various insulation qualities in addition to carbon footprint and R-value. For example, without accounting for air barrier and water barrier effectiveness, there is a potential for disaster, primarily in the form of condensation and consequential mold growth, but also in other ways. On the Enclosure Team here at SWA, one of our chief tasks is to understand the complex interaction of all the factors surrounding insulation (or any material) choice and to advise architects and owners of the hidden dangers of certain choices and the best options for any condition.
Carbon Footprint Analysis (a sub-set of LCA) takes into account all the carbon emissions (greenhouse gases put in the atmosphere), associated with a building or material from cradle to grave, i.e., to the point of recycling or disposal, and includes both embodied and operational carbon emissions. There is a growing number of firms that are now specializing in this type of analysis, which is increasingly available to building industry professionals, government officials, owners and manufacturers. Furthermore, as the concepts and facts upon which LCA and carbon footprinting are based are becoming more familiar, building professionals can now take advantage of the several computer applications that have been developed to assess and compare the carbon value of building materials and processes. Examples are Athena, LCA One-click, Tally, and most recently EC3. Our buildings are complex, and so is the mathematics behind them. Getting a big picture sense of what’s hot and what’s not, of relationships and proportions, will allow us to make much better decisions at design conception, inception and throughout design and construction, which will ultimately impact the course of climate change.
Whenever we build new, we have an opportunity to design any assembly and choose from a variety of materials. If we decide that certain materials are no longer acceptable options, we have other options. With design forethought, we can eliminate HFC-blown XPS and SPF from new construction. Insulation is the tip of the (melting) iceberg; however, the structure and cladding of a new building accounts for roughly 80% of its embodied carbon.
In the larger picture, most new buildings – even operational net-zero buildings – rack up a huge carbon debt, directly adding to the carbon load in the atmosphere before the lights are turned on. And, this is compounded if an existing building is destroyed to make way for the new. Consequently, there is growing realization and acceptance that the building that already exists is the greenest building, amply demonstrated in the groundbreaking study with that title published a decade ago by The Green Lab of the National Trust for Historic Preservation. From an LCA/embodied carbon point of view, the logical conclusion is that the conservation and reuse of existing buildings should be prioritized over new construction.
Because the embodied carbon debt of older buildings has already been paid down or off, older buildings represent an unparalleled opportunity for carbon savings, especially if they are retrofitted to lower their operational carbon, so there may still be a role for HFC-blown XPS insulation products. Such products may be the best solution for particular conditions because of the unique combination of thermal, moisture and air management benefits of these insulations. Then the savings from not demolishing a building and not building new may offset the proportionally small carbon expenditure of the insulation material itself. The new and improved tools for quantifying embodied carbon coming online will increase our understanding of embodied carbon and our decision-making processes.
It is easy to become overwhelmed by the enormity of climate change and the complexity of our operations that feed it, but there is an athlete’s maxim we should remember, resistance is greatest when closest to the goal. We may feel that we have been making an effort for decades, yet still there is so much waste, and the carbon line continues to goes up. Perhaps we should take a moment to recognize how far we have come, what we have achieved, how much we already have put in place, and how close we really may be to our goal. It is a matter of persistence, of heart and will, and we can do it.
All hands on deck!
Contributor: Catherine Paplin, Senior Building Enclosure Consultant
Steven Winter Associates