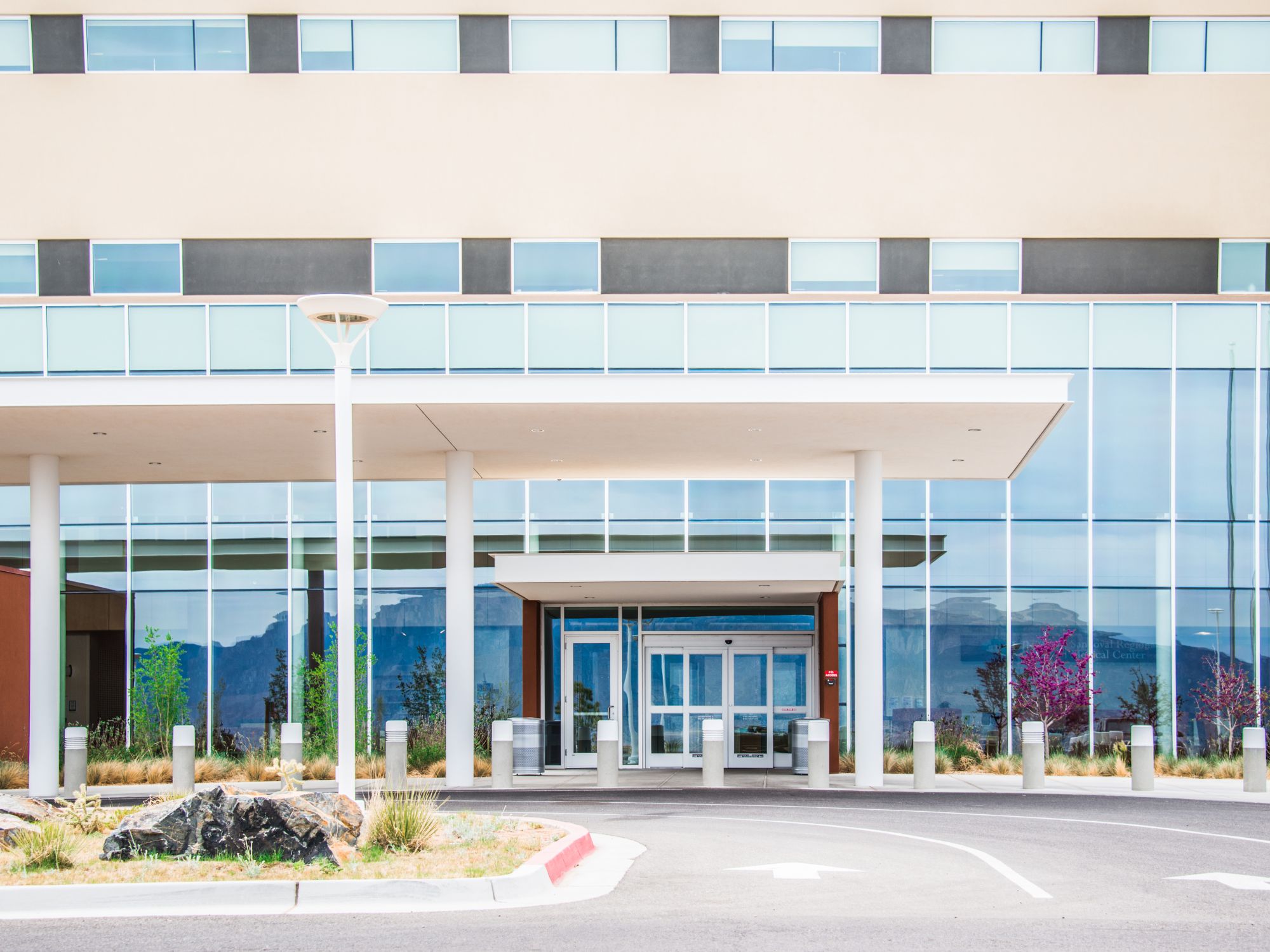
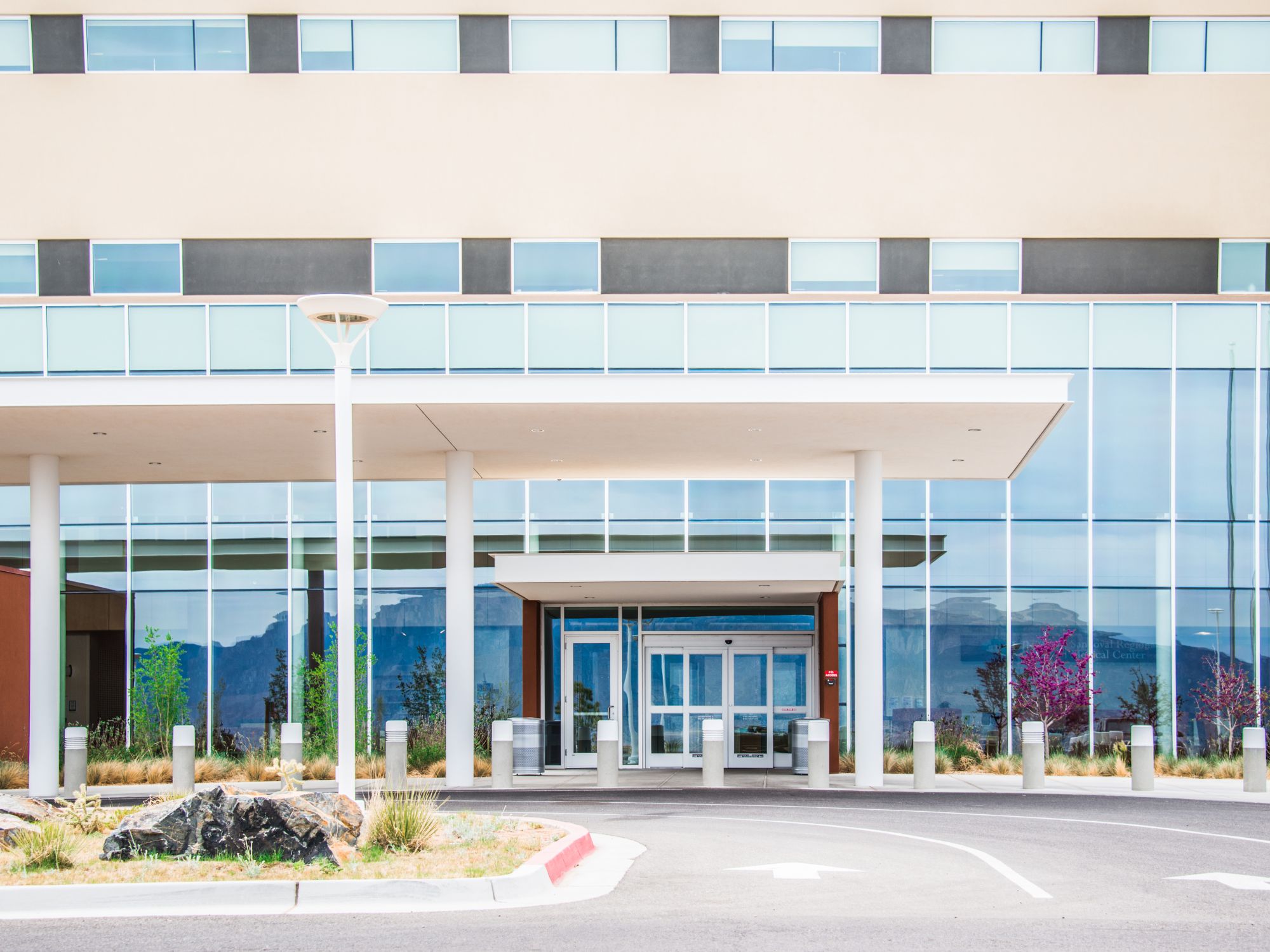
Blog
The future of green building is here, and it’s more carbon-conscious than ever.
LEED v5 represents a significant evolution in sustainable design standards. The changes are substantial yet offer flexibility and aim to raise the bar considerably in several key areas.
Fifty percent of the updated rating system is now focused on decarbonization-related credits and prerequisites, 25% dedicated to quality of life (health, equity, and well-being) and 25% on ecological protection and restoration, i.e., biodiversity.
Embodied carbon refers to the Global Warming Potential (GWP) of building materials like concrete, steel, wood, glass, insulation, gypsum, etc. GWP is expressed in units of kilograms of CO2 equivalents, or kgCO2e.
The Reduce Embodied Carbon credit under Material and Resources rewards the reduction of GWP in the building structure, enclosure, and hardscape material with a maximum of 6 points, which is a step up from earlier versions of LEED.
To navigate the changes within LEED v5, it’s important for teams to focus on early stage planning and goal setting. It’s also essential to take a lifecycle approach to decision making—considering not only the carbon impact of materials upfront, but accounting for circular opportunities, like recycling building materials back into the supply chain.
Read on for more details about how to navigate the updates related to embodied carbon reduction with the launch of LEED v5 in April.
There is a new prerequisite to assess and quantify embodied carbon. Exploring material options for the structure early on is one of the most significant areas teams can focus.
In the concept or schematic phase, the requirement is for a sensitivity analysis—or Carbon Hotspot—which emphasizes the structural engineer’s role early in the design to discuss impacts from the superstructure.
Project teams can choose from many free carbon calculators like EC3 or Athena to do the required hotspot analysis, which aims to identify the top three material contributors.
A whole-building Life Cycle Assessment (wbLCA) is not required at this stage (though SWA can provide this for projects targeting the 6-point credit).
It’s important to note that while projects can register for LEED v5 now, it can take several months to be fully up and running. We recommend a simple feasibility study for new projects or projects interested in transitioning to v5 from earlier versions. This step gives project teams time to familiarize themselves with the new requirements and adjust their strategies accordingly.
Reach out to SWA for your next LEED project.
Quantifying the impacts of structure, enclosure, and hardscape materials, as well as documenting cradle-to-gate emissions, is required for all LEED v5 projects.
Products to pay attention to include low-carbon concrete, mass timber, engineered wood, bio-based insulation materials, and salvaged and reused materials.
Other important materials to consider include ceiling tiles, gypsum wall board, and paint due to their notably high carbon footprint.
Mechanical systems are not required yet, but the industry is making progress on quantifying the embodied carbon associated with them. However, low-carbon refrigerants are readily available and mandated in some jurisdictions.
One of the most notable changes in LEED v5 is the ability to get more points with a wbLCA.
wbLCA tools use environmental data sources and material-level information from Environmental Product Declarations (EPDs)—the standardized documents that provide transparent information about the environmental impacts of products, including their GWP. This approach will encourage project teams to consider the environmental impact of materials from extraction and manufacturing through to end-of-life scenarios.
Along with material choice, LEED v5 also addresses carbon emission reductions in the construction phase. Points can be awarded for tracking jobsite emissions within the new Reduced Embodied Carbon credit, which specifically targets fuel and utility usage.
Encouraging low-carbon construction processes further emphasizes the need for carbon-saving strategies at all stages of a project.
LEED v5 introduces more stringent requirements for EPDs The EC3 tool is an essential resource for locating EPDs, though there are other resources like Ecomedes and UL Spot.
V5 prioritizes reductions of the most carbon-intensive materials, such as concrete, masonry, and steel. The Reduced Embodied Carbon credit awards additional points for choosing specific materials with reduced GWP.
By prioritizing materials with lower carbon footprints, LEED v5 is pushing manufacturers to be more transparent and innovative in their processes.
Teams can choose either material optimizations or wbLCA, allowing more innovative teams to claim more points with the wbLCA while giving a prescriptive pathway for projects.
Recognizing that the greenest building is often one that already exists, LEED v5 offers more points for projects that preserve existing structures, thereby avoiding the significant embodied carbon associated with new buildings.
LEED v5 decouples building reuse from the new construction focused credits. It rewards projects that reuse building materials and structures.
As we move towards a more carbon-conscious built environment, the larger focus on embodied carbon in LEED v5 represents a significant step forward. By providing a clear framework for measuring, reporting, and reducing the carbon footprint of buildings, the program offers more options and pathways to suit a variety of building types and project teams.
This flexibility will help drive the industry towards more sustainable construction practices and a more climate-resilient future.
The goals are ambitious. Ultimately, the rollout and the ability for project teams to streamline documentation without significant increases in time and resources to reach certification will influence how the market adjusts to the new rating.
LEED v5 is open for project registration. It’s time to prepare your teams for the increased emphasis on embodied carbon reduction.
SWA is here to help. Our consultants work with project teams from the concept and schematic design phases through construction to help them meet their embodied carbon goals. We perform Hot Spot Assessments and Whole-Building Life Cycle Assessments to assess and document opportunities for embodied carbon reductions. Click here to contact us.
Contributors: Kai Starn, Senior Sustainability Consultant
Steven Winter Associates