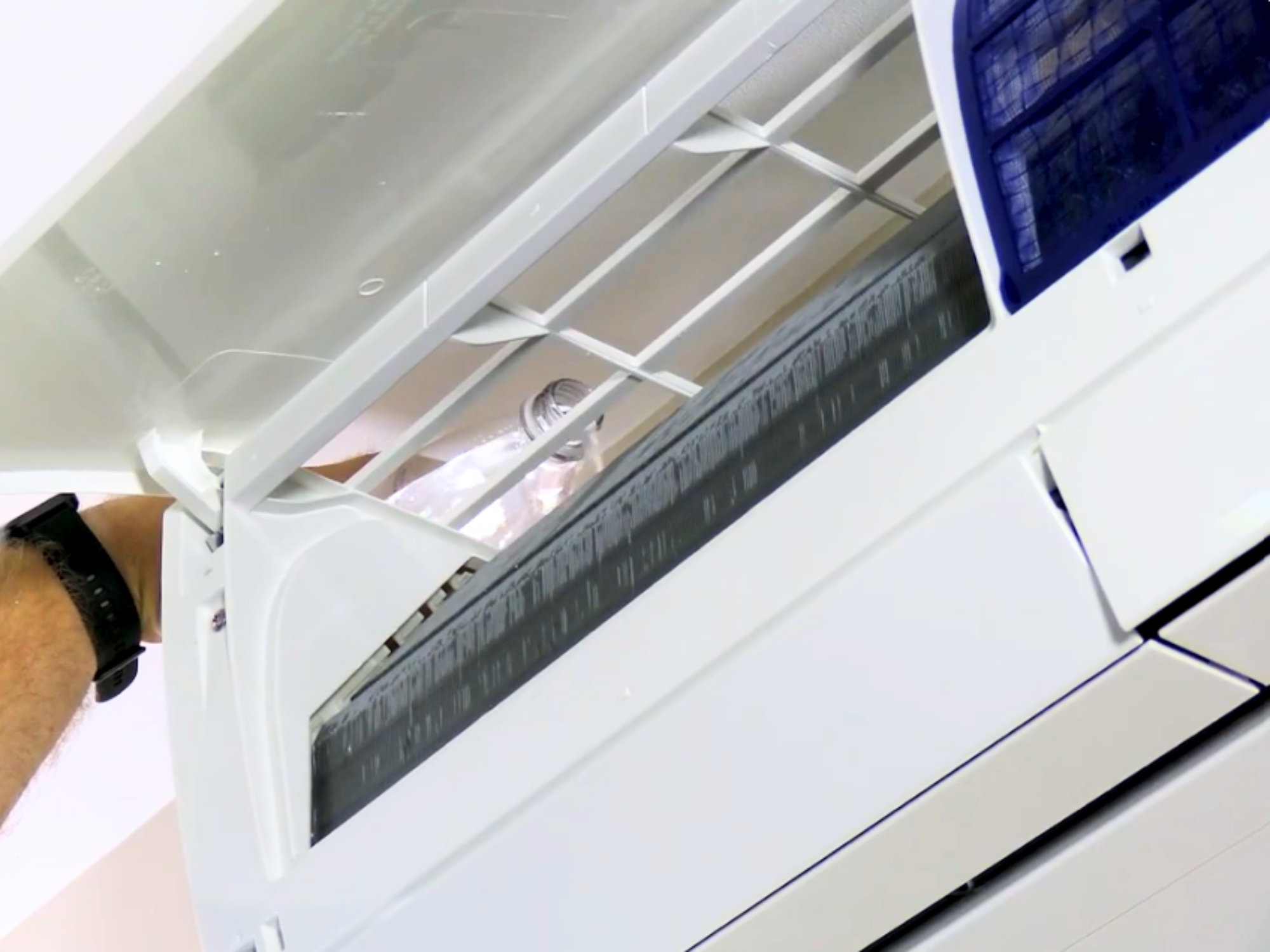
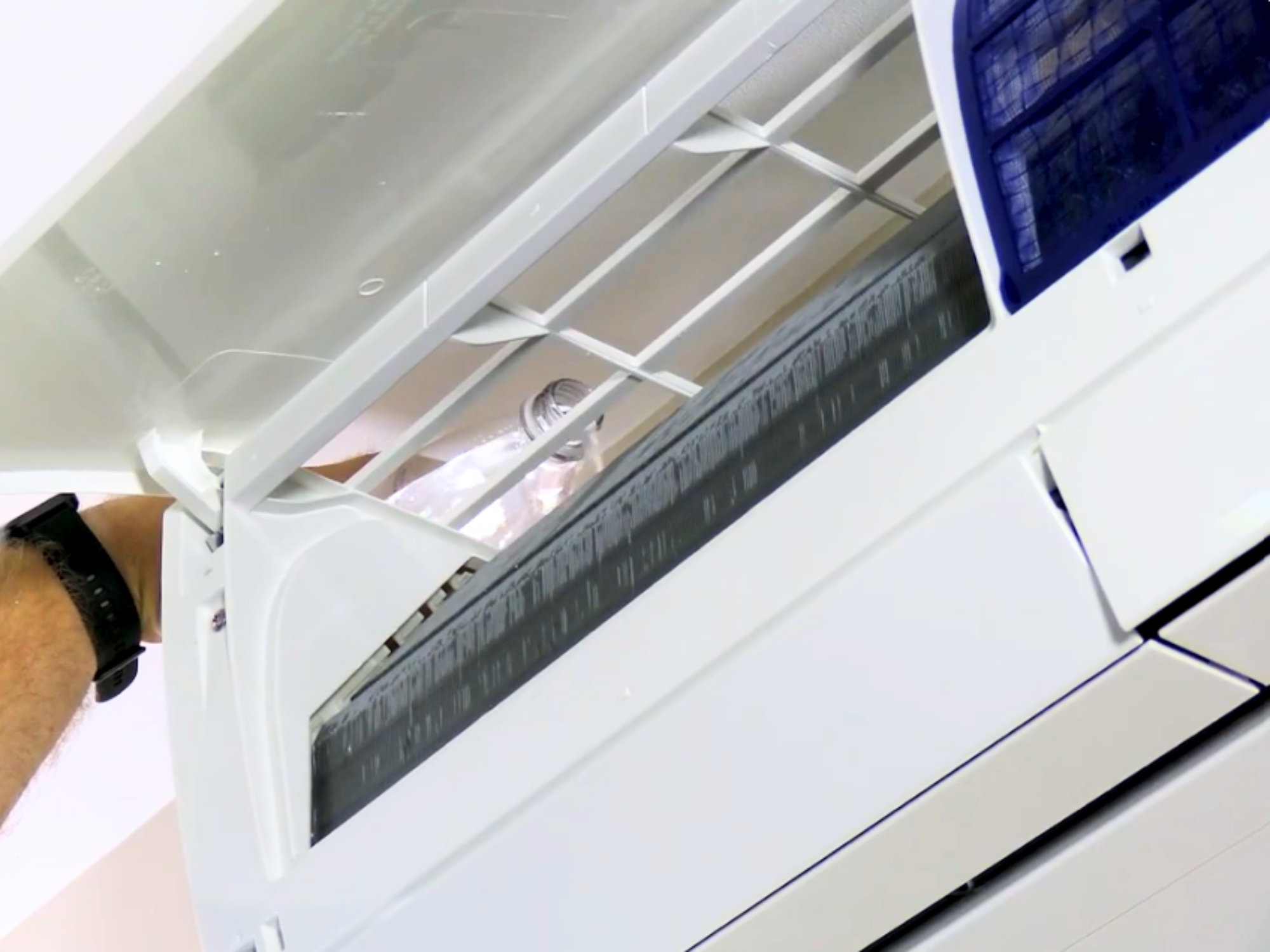
How to Install an Air-Source Heat Pump
Whether you’re new to heat pumps or need a quick refresher, this video series demonstrates each step of how to install an air-source heat pump system optimized for efficiency and comfort in colder climates—which is critical to widespread adoption.
Read