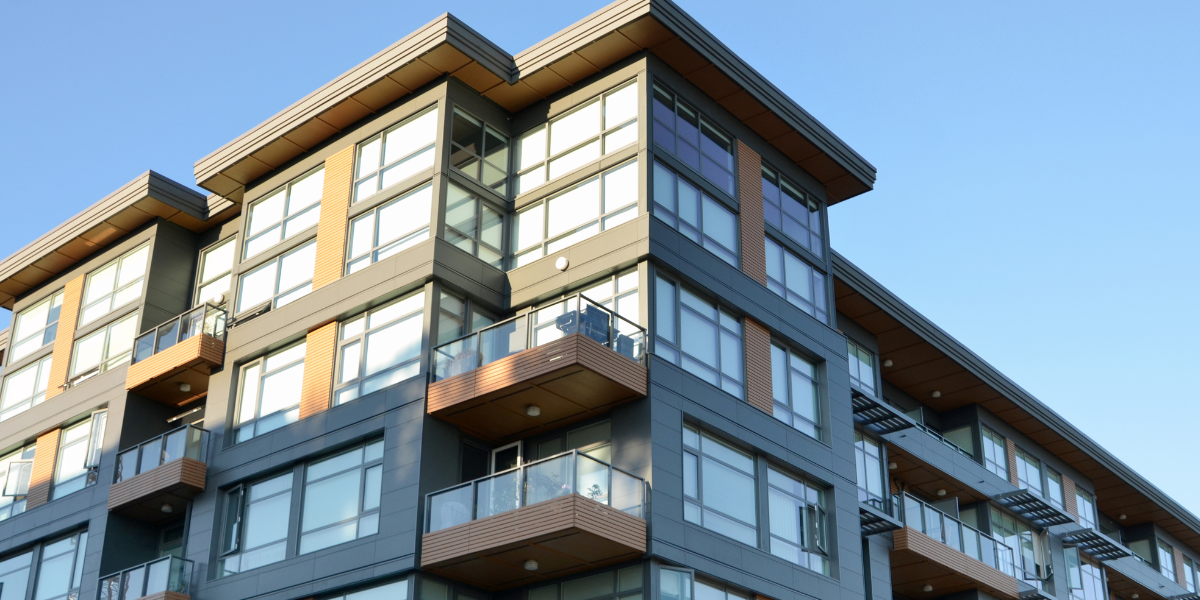
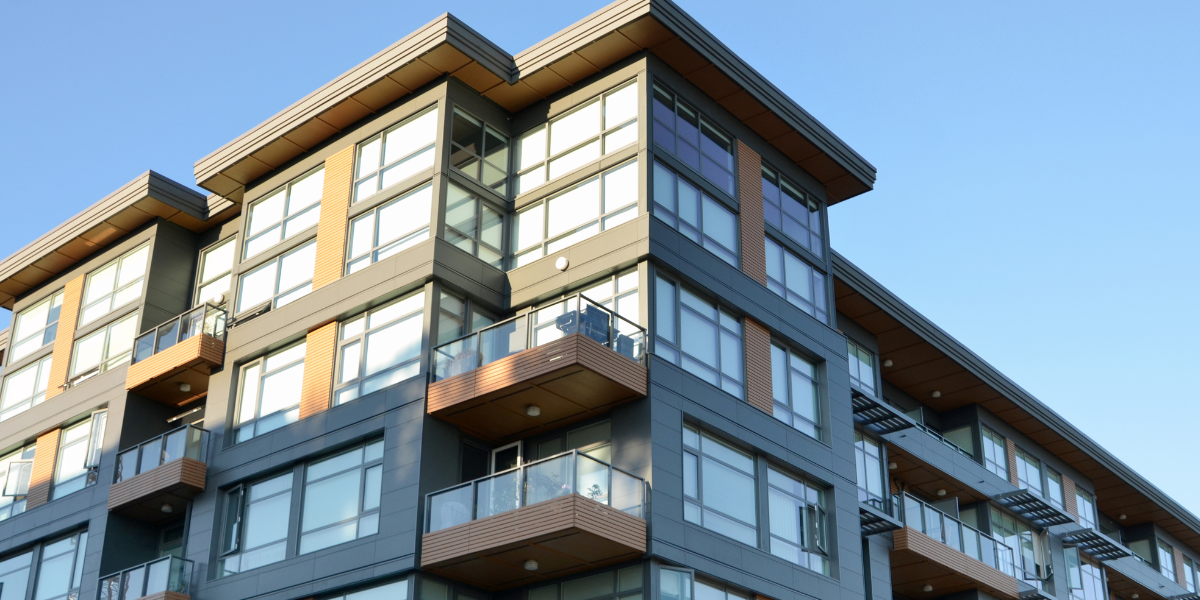
Blog
Installing a dedicated domestic hot water (DHW) plant is a common energy conservation measure (ECM) in the New York City multifamily market.
According to Local Law 87 data, approximately 80% of the audited multifamily floor area uses steam heating boilers to produce domestic hot water.1 A recent SWA analysis of data from steam buildings with tankless coils that implemented this ECM suggests that auditors may want to think twice about recommending this measure widely.
Two unsupported arguments are typically made in favor of installing a dedicated DHW system:
A condensing water heater operating under ideal conditions can achieve combustion efficiencies greater than 95%, notably higher than the typical efficiency of Scotch marine boilers. However, ideal conditions for a condensing water heater require a low inlet water temperature and low firing rate – the nameplate high efficiency is not an automatic feature of the product itself.
When water heaters and potable storage tanks are installed in a dedicated DHW plant, the storage tank temperature must be maintained at a minimum of 140°F to prevent Legionella growth. Water from the tank is blended with makeup cold water and recirculation water and cycled through the water heater to charge the tank. SWA analysis of BMS sensor data from multiple dedicated DHW plants showed that this blended inlet water temperature typically varies from 120°F to 140°F. This puts the equipment outside of the high efficiency operation range. An inlet temperature of 130°F results in a roughly 87% combustion efficiency in a condensing water heater per ASHRAE.2
Inefficiency results from two main conditions: combustion losses and off-cycle losses. In New York City the DEP requires a minimum 83% combustion efficiency for oil-fired boilers and 80% for gas-fired boilers. SWA regularly tests boilers operating above this floor. SWA also recently studied the average off-cycle losses in a few typical Scotch marine boilers as part of a NYSERDA-funded study evaluating linkageless burner technology. Off-cycle losses, comprising jacket, flue, and purging losses, were measured from 0.5% to 4.5%. A value of 2% is achievable with tuning and use of draft controls.
For the purposes of this discussion, we posit that with routine maintenance and care Scotch marine boilers typically have an 83% combustion efficiency with 2% off cycle loss, for a typical seasonal efficiency of 81%.
Heating boilers are sized to provide comfort on the coldest days and are typically oversized on top of that. The DHW load in a multifamily building is a small fraction of that peak heating load, so a heating plant is always going to be oversized for DHW production. An oversized boiler will fire more often than a boiler that is appropriately sized for its load.
It does not follow, though, that a large heating boiler will short cycle to produce DHW. SWA analyzed BMS data on boiler firing rates for several combined-plant buildings with tankless coils for DHW production. During heating season, we see that boilers almost always fire to satisfy a call for heating; it is very rare for a boiler plant to fire because the DHW load needs to be met. Separating the heating and DHW loads will not reduce short cycling if the boiler does not cycle for the DHW load to begin with.
The following chart shows one day of a typical control firing boiler on a regular cycle. Every time the control fires the boiler, the stack temperature rises (red line) and the steam pressure rises to its 7 psi setpoint (blue line). If the system was firing to meet a DHW demand, there would be erratic firing during times of higher DHW demand and the boiler would fire to raise its kettle temperature without producing steam. Instead, we see the boiler firing regularly with its timed heating call, with DHW provided while the boiler coasts between cycles. Off cycle losses can therefore be entirely allocated to meeting the heating load and not debited against DHW production efficiency during the heating season.
Outside of the heating season, the boiler plant is only firing for DHW production. This is the season when a heating boiler is most oversized. However, Scotch marine boiler kettles have a large storage capacity and can hold enough heat to satisfy hours of DHW load. This storage mitigates short cycling by allowing the boiler to fire only when needed to boost the kettle above the temperature needed for tankless coil operation. The boiler does not fire to meet the DHW load at a given time; the boiler fires to meet the full load of heating up its large kettle.
The following chart shows this theory in practice. BMS data was analyzed for a typical site with aquastat control on a Scotch marine boiler for summer firing control. The aquastat is set to fire the boiler when the kettle drops to 168F, and to cut out when the kettle is heated up to 198F. The red line in the graph is the kettle temperature over one typical summer day. The temperature climbs every time the boiler fires, and then drifts back down as the tankless coil pulls heat out for DHW production. This boiler only fired 13 times in the 24-hour window shown, with no short cycling at all. This aquastat could even be set for a larger temperature band to further decrease the number of firing cycles per day.
SWA analyzed pre- and post-retrofit utility data for nine sites that installed dedicated DHW plants. The utility data was adjusted to hold heating fuel use constant. This is because almost every building also implemented a fuel conversion and/or heating system improvement in parallel with installing the dedicated DHW plant, and the savings from that heating improvement work would confound the analysis of the impact of the dedicated DHW plant installation. The following graph shows this adjusted fuel use normalized by building size, where the DHW loads calculated from regression analysis are combined with the weather-normalized constant site heating load. Site #7 is a campus-style complex, but the others are all single steam buildings with Scotch marine boilers and tankless coils.
Fuel usage did not improve greatly with the dedicated DHW plant installation at the individual sites; only the campus site (#7) showed noticeable improvement. DHW fuel usage actually increased for some buildings. A possible explanation of this is because most of these buildings undertook other scopes of work at the same time as installing the water heaters. By introducing these additional factors, exceptionally poor performance can occur due to negative cross-scope interactions or by poor design or installation.
Assessing the two arguments in favor of this measure does lead us to expect limited savings at best. The pre-retrofit Scotch marine and tankless coil plants would have been producing DHW at roughly 81% efficiency in the summer and 83% efficiency in the winter. The new dedicated DHW plants likely operate at 86% efficiency (87% combustion efficiency with 1% off-cycle losses estimated). This gain of 5% for 33% of the year and 3% for 66% of the year only works out to a 3.7% savings on DHW fuel use if the new plant runs year-round. Utility analyses typically show that annual heating fuel usage is about twice DHW fuel usage, which means that this savings would equate to a reduction of only 1.2% on central plant fuel bills, assuming the construction and commissioning is completed very well.
In addition to overestimated savings potential, this ECM is also notorious for underestimated installation costs. New water heaters typically cannot be common vented with the existing Scotch marine boilers. A new flue can cost roughly $10,000 per story of building height. ConEd offers a discounted gas rate for equipment that is only run for the summer months, but the cost of installing the extra gas infrastructure can outweigh the potential rate savings. One argument for installing a dedicated DHW plant is to right-size for the load, but most designers use industry sizing tools that grossly overestimate the capacity needed. Inflated load calculations lead to high first costs of water heaters, upsizing of gas piping, larger flue sizes, etc., all of which drive ECM cost up.
There are some scenarios in which this measure can have a payback less than the equipment lifetime, but those are rare cases. Some sites have short venting route options, campus steam distribution networks that limit the efficiency of a combined plant, low costs for installing a dedicated gas line to take advantage of ConEd’s summer gas rate, and/or use expensive fuels for the boiler plant but would be able to put the dedicated water heater on cheaper gas. These are all relatively uncommon cases in our building stock.
Historically, this measure has looked more promising due to the high cost of oil. Just a couple of years ago many NYC buildings were paying more than one and half times what they pay today for oil. Analyzing the payback of a dedicated DHW plant against an historical oil baseline cost can bring payback below 15 years. What we see is that many of our client’s complete oil-to-gas conversions when they install the new DHW plant, so gas becomes the correct baseline against which to calculate savings. That can double or triple the payback of the new dedicated water heater.
Installing dedicated DHW plants has a low savings potential in individual buildings and a high capital cost to execute. There are other measures to invest in that confer more savings and better align with the City’s 80×50 climate goals. For example, the market is beginning to attract more air-to-water heat pump options, and new controls approaches can electrify DHW production during low-cost periods with time-of-use electricity rates. The old dedicated gas-fired DHW measure appears to be flawed, and we are seeing promising new technologies to pursue in its place.
Contributor: Nicole Ceci, Principal Mechanical Engineer
Steven Winter Associates